WHAT IS SIRIM DPio?
SIRIM Digital Production Management System (SIRIMDPio™) is a comprehensively customized Manufacturing
Execution System (MES) that develop to fulfill the need
of Malaysian Small-Medium-Enterprise (SME) companies
toward adoption of Industry 4.0.
SIRIM-DPio™ is a cloud-based and real-time monitoring
system, that visualized via digital dashboard system and
smart mobile application to digitalised production
management process.
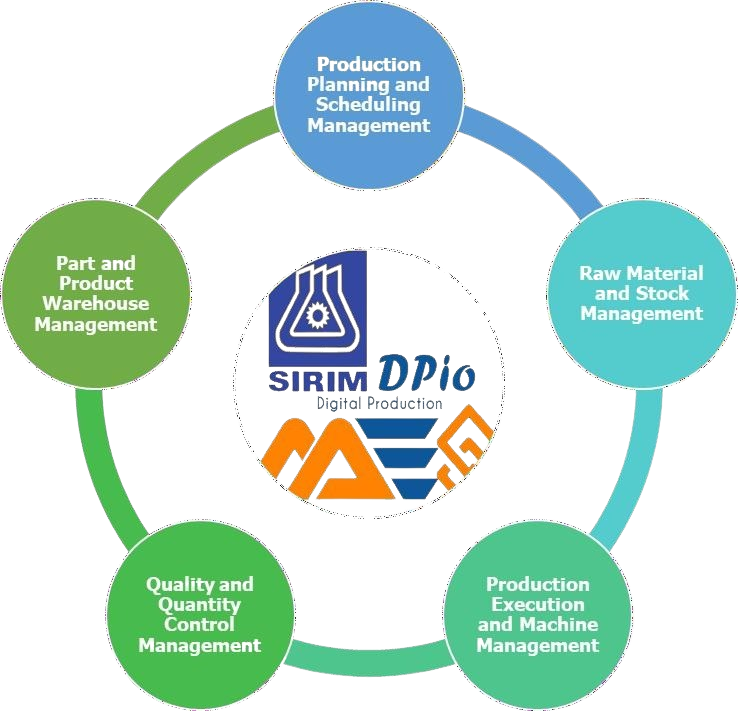